By Fred Vergnères
Sustainable aviation fuel, or SAF, has come into wider use in recent years, notably in the business aviation industry, in response to steadily rising customer demand. Given its environmental impact and media attention, Ultimate Jet sat down to talk with Joël Navaron, President of TotalEnergies Aviation, to learn a little more about this sustainable fuel.
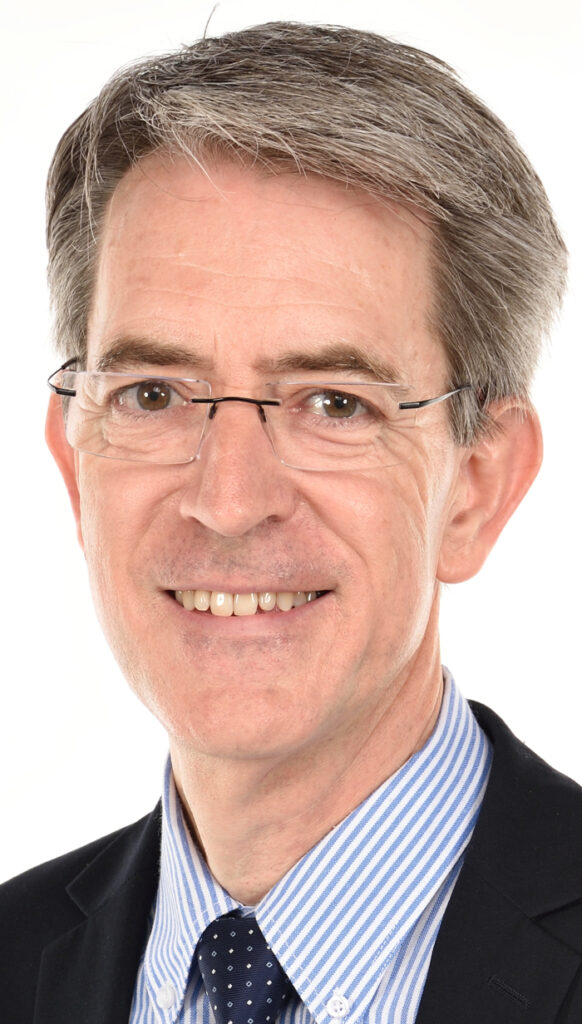
Could you briefly tell us where sustainable fuel comes from?
SAF is a blend of pure SAF, meaning biofuel and/or fuel derived from the circular economy, and Jet A1 fuel. We now have seven different processes for manufacturing pure SAF, as well as a co-processing process for SAF. Those eight processes have all been approved by ASTM International, formerly known as the American Society for Testing and Materials, and there are additional processes now awaiting certification.
HEFA—Hydroprocessed Esters and Fatty Acids—is the most mature of those processes from an industrial standpoint. Fuels made by other processes, such as Alcohol-to-Jet (ATJ) and Fischer-Tropsch (FT) fuels, are still in the research phase and aren’t yet ready for full-scale production. So in most cases, when we’re talking about SAF we mean HEFA fuel, primarily produced from used cooking oil and animal fats.
Currently, this pure HEFA SAF can only be blended with jet fuel at up to 50%, largely for reasons of engine compatibility. But very recently, under specific conditions, we’ve seen some initial test flights conducted with 100% SAF. Safran Helicopter Engines and Airbus Helicopters, for example, have both carried out flights using our products.
What’s the real environmental impact of a fuel like that?
Pure SAF emits 90% less CO2 across its entire lifecycle than a fossil-fuel equivalent. All of these processes are authenticated and certified by independent bodies, such as ISCC (International Sustainability and Carbon Certification). ISCC not only certifies the complete production chain, it also certifies that the source feedstock is in proper compliance.
What production channels are currently being used?
Europe has very little in the way of organized networks for collecting used cooking oil. That’s something that really needs to be put in place. A few countries, such as Belgium, have taken the lead in that area to some extent. It’s a significant challenge if we’re going to meet future demand for SAF.
Fifty thousand tons of pure SAF were produced worldwide in 2020. In consumption terms, that’s not very much compared to a jet fuel market that totaled some 170 million tons that same year (and 330 million tons in 2019).
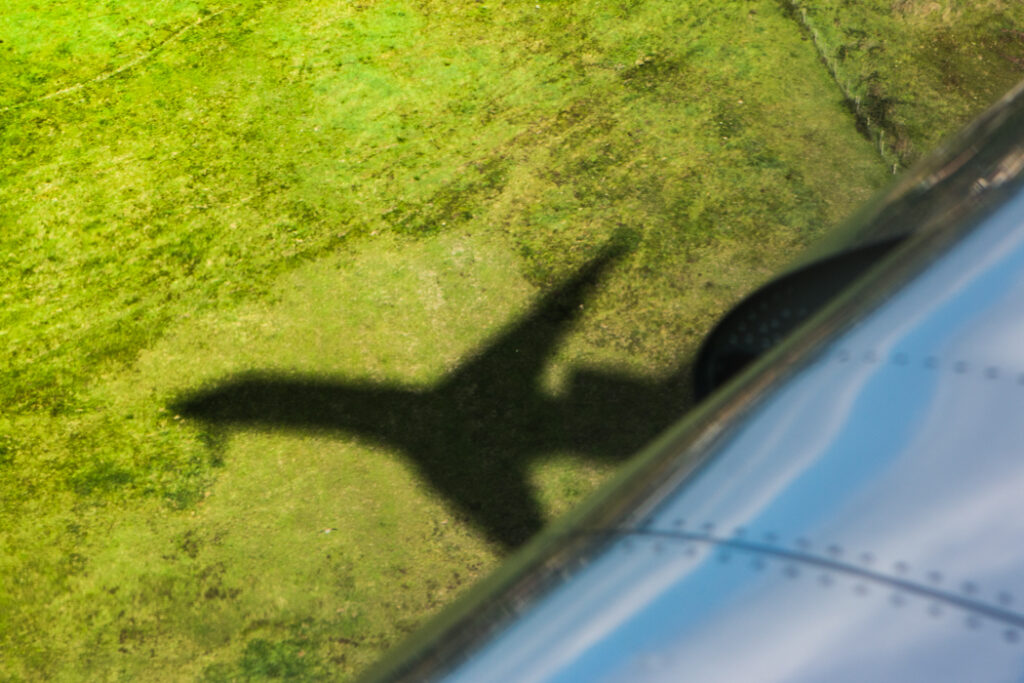
Where do you currently produce SAF?
Currently, the product we sell is produced in France, first at our La Mède refinery near Marseille and then at our Oudalle facility in Normandy. By the end of 2024 we’ll be producing 170,000 tons of pure SAF at our Grandpuits biorefinery just south of Paris.
How are you distributing this sustainable fuel to facilities? What are some of the airports around the world where it’s already in use?
We’re able to transport the fuel by road to the various airports that ask for it. But it’s important, for both environmental and financial reasons, that we consolidate our distribution at a few major platforms. For now we have two special facilities in place, one at Paris-Le Bourget Airport and another at the Clermont-Ferrand airport.
What percentage of SAF is blended into the fuel delivered to operators at Le Bourget and Clermont-Ferrand?
Pure SAF makes up 30% of the blend we deliver to both airports. That’s what our business aviation customers are requesting. But the percentages can change for certain specific operations and test flights.
Are you seeing a real increase in demand for SAF among operators, particularly in business aviation?
The demand in business aviation is growing steadily. Our customers have set ambitious targets, and we’re very proud to be able to support them in their efforts to reduce their carbon emissions.
What would be needed to be able to use more than 50% SAF to power a flight?
As I mentioned, pure SAF obtained using the HEFA process can be blended at up to 50%. That’s not the case with every process that’s been certified. Pure SAF from HEFA specifically has three important attributes:
– A lower density than Jet A1 fuel.
– Lower lubricity.
– Zero aromatic content.
These three characteristics have a very real impact on normal engine operations. For example, aromatics ensure that the engine seals perform at optimal levels. At 50%, you don’t need to make any modifications to the aircraft’s infrastructure, engines or subassemblies. But above that level, you need to automatically test that every assembly is working properly and verify that your use of the fuel is compatible with the plane’s systems. So engine testing is currently underway at a number of engine and aircraft manufacturers, including Safran and Airbus.
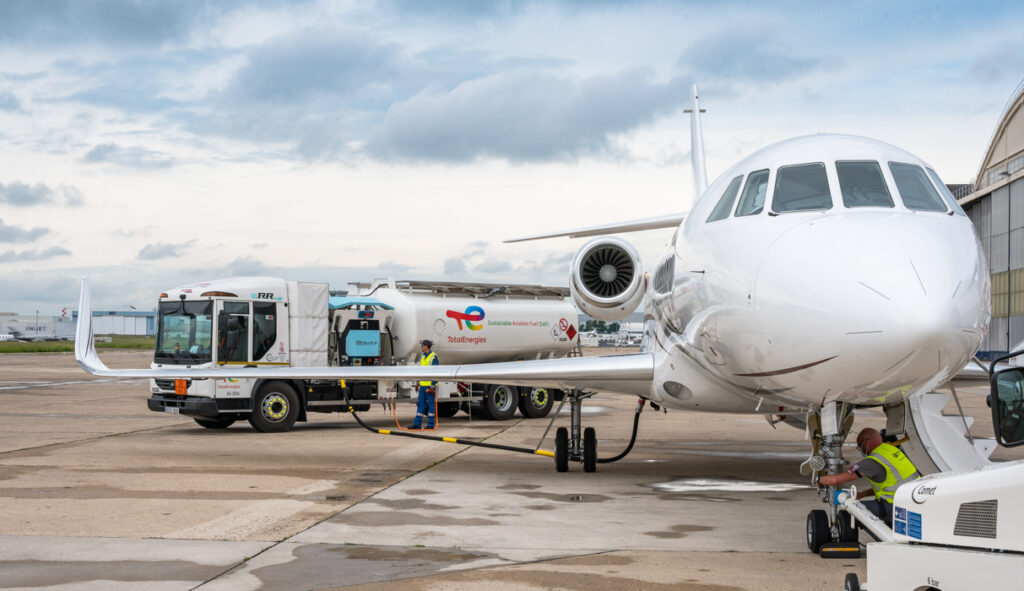
How long will it be before you can produce a fuel that’s less expensive than today’s SAF?
Our ambition at TotalEnergies is to supply the world with the energies it needs and ensure those energies are ever more affordable, clean, reliable and accessible to as many people as possible. Those goals are very important to us. Our aim of getting to net zero in our operations by 2050, together with society, is really a guiding principle behind our strategy. SAF is part of that transition in every way, and our ambition is to make it as affordable as possible. Wider use of SAF will reduce our customers’ CO2 emissions and help ensure they can meet expectations. Price will be one of several important factors in that process.
To answer your question, it’s important first of all to note that both pure SAF and Jet A1 fuel are intrinsically changing in major ways. Moreover, the prices for both those products have been fluctuating a great deal as well. That said, on average HEFA fuel has typically been about four to five times more expensive than Jet A1 fuel. The price hinges primarily on the cost of collecting used cooking oil and the logistics involved.
European Union regulations rule out vegetable oils. So the industry has been turning to feedstocks from the circular economy, such as used cooking oils, animal fats, lignocellulosic biomass, forest residues and household waste. Some of those feedstocks are still not widely available, and collecting them is no easy task.
So in order to expand production of sustainable aviation fuels and reduce their cost, we need to work hand in hand with specialist businesses to establish a real network for collecting waste and residues, but we also have to work on diversifying the feedstocks we use.
At the same time, governments need to help with this transition. Several jurisdictions, including the state of California in the U.S. and the Netherlands, have adopted incentives to encourage the use of SAF. Norway and Sweden, among other countries, have introduced minimum renewable content requirements that took effect in 2020 and 2021 respectively. A similar mandate just came into force in France on January 1. There’s a lot of momentum.
Might the use of other processes have an impact on cost?
Processes such as gasification/Fischer-Tropsch (where production involves so-called advanced feedstocks such as farming or forest residues or municipal waste) and Alcohol-to-Jet—a process that promises substantial flexibility when it comes to feedstock, including industrial gases and the lignocellulose used in ethanol production—require a high level of investment for commercial production on a large scale. Consequently, the cost of the end product would be six or eight times higher, which doesn’t take us in the right direction.
Then there’s e-fuel, meaning synthetic fuels produced from hydrogen, ideally derived from renewable power and carbon dioxide captured from ambient air or industrial wastewater. E-fuel would be about 10 to 12 times more expensive than today’s Jet A1 fuel. Those technologies are still in the R&D stage and extremely costly, but over the longer term they could represent a promising alternative.
Do aviation manufacturers have a role to play in helping you develop these new fuels?
Despite these hurdles, we’re seeing the entire aviation industry—engine and aircraft manufacturers, airlines, energy suppliers—all mobilizing to develop these new industries for sustainable aviation fuel. And there’s also a host of new initiatives, notably in the form of public/private partnerships. It’s by working together that we can successfully develop these new fuels, which are essential to achieving the goal of net zero emissions by 2050 across the entire aviation industry.