By Sylvie Péron – ©Comlux
As the exclusive partner of Airbus for the first 15 ACJ TwoTwenty cabins, Comlux Completion delivered the second completed aircraft. «Just eight months after the first ACJ TwoTwenty left Comlux completion and maintenance center in Indianapolis and entered into service, the second one is being delivered to the end client now, while cabin outfitting of the third ACJ TwoTwenty is in full swing and planned to be finished by end of 2024. In addition to that, the fourth ACJ TwoTwenty arrived for completion at the end of February, and started its cabin outfitting as soon as it reached our facilities. From 2025 onwards, we are targeting to deliver 4 to 6 ACJ TwoTwenty cabins per year,» said Richard Gaona, Comlux Executive Chairman and CEO. Comlux Aviation is operating the aircraft, registered in Malta. 9H-22OCJ will be available for limited charter.
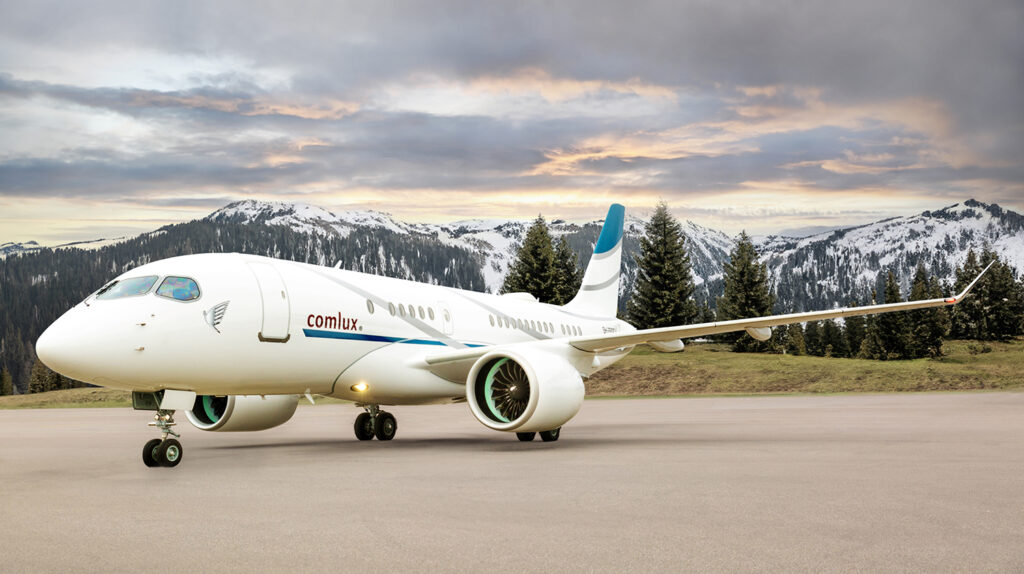
«For the second ACJ TwoTwenty, the customer wanted a cabin configuration more focused on their corporate needs. While keeping the modern design styling of the ACJ TwoTwenty more classic elements were mixed in,» said a company spokesperson.
This second aircraft features an additional galley in the middle and the private suite in the back has two couches facing each other that extend into two single beds. Furthermore, this aircraft has wall-mounted TVs and leather seats. And of course the material selection is different on each aircraft.
Considering most industries suffer from supply chain problems, Comlux has indeed faced some supply chain challenges. «However the teams of in-house craftsmen produce a lot of items directly in the facilities and so the supply chain issues although being challenging are not something that would put the TwoTwenty program at risk» says the company.
Comlux’s completion facility in Indianapolis is equipped with CNC technology allowing producing parts in-house. In addition to that, a reliable cooperation has been established with the TwoTwenty key suppliers.
Comlux Completion recently worked extensively with the Indiana State government to sponsor training programs. «Taking a long-term strategic approach to this current problem is essential to ensure continuity, without facing any shortage. Skill sets most needed are cabinet-makers, electrical wire fabrication specialists and not necessarily aircraft mechanics. Indiana has been extremely eager, and supportive to help get these programs going,» continues the spokesperson.
Purpose-built to serial production
Comlux Completion’s main facility is located at Indianapolis Airport, which is open 24/7 and very supportive when test flights are needed. At over 157,000 sqft (14,600 sqm), every square inch was built to craft the finest VIP interiors in North America. While most Completion Centers have migrated into existence from focusing on MRO work to incorporating some VIP developments, the entire vision behind Comlux was to focus on completions first. The impressive hangar area can accommodate up to 5 narrow-body aircraft or 3 narrow-body and 1 wide-body aircraft.
Past the receiving warehouse there are two straight hallways. One goes directly to the hangar for the turnkey products manufactured by outside partners, and the other goes down the back doors of all the production facilities in the hangar. This facility was designed for machining, fabricating, crafting, finishing, and installing VIP interiors without ever stepping outside these hallways.
The changes in the business model and success of multi-year projects like the ACJ TwoTwenty had initially raised concerns about the facility’s initial single project based layout. Migrating from project-based design (one year & one project with unique configuration) to program (multi-year & multi-projects with similar configuration) required fundamental changes to business processes and significant increases in internal capabilities.
However, even with this change, it was evident that being set up as a completion center first and not an MRO allowed expanding offsite in certain shops without missing a step. Now, the traffic of the turnkey hallway even contains parts manufactured in an offsite facility that go straight to the aircraft. Comlux added the 10,000 sqft (929 sqm) facility in Q4 of 2023 and is looking forward to further expanding in 2024.
Additionally, Comlux Aviation division allows access to operational teams (crew, flight service engineers and CAMO specialists).
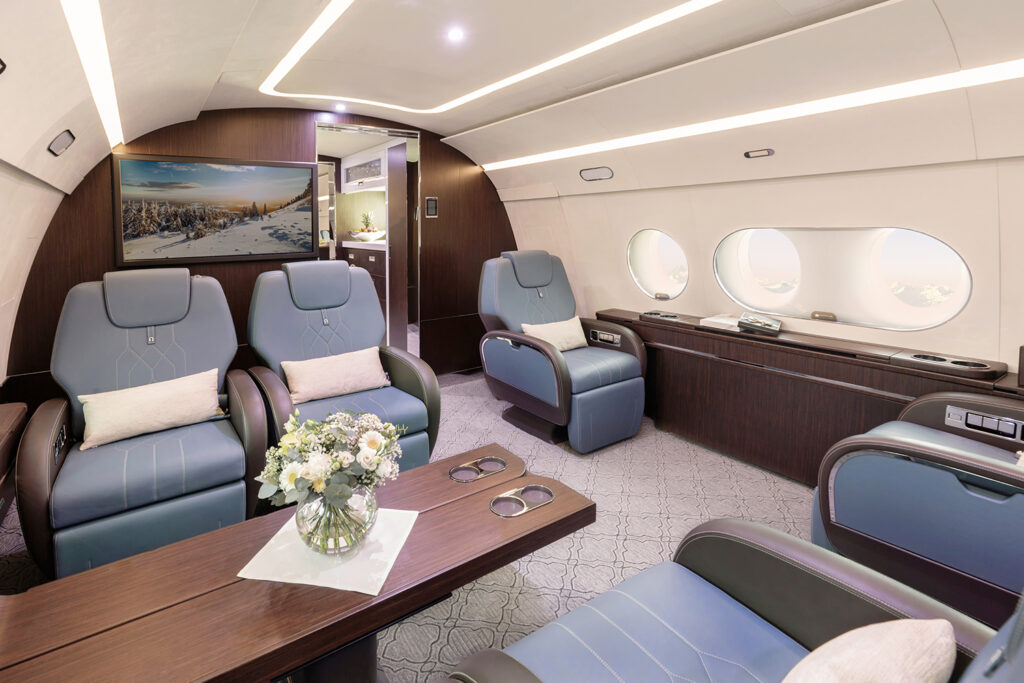
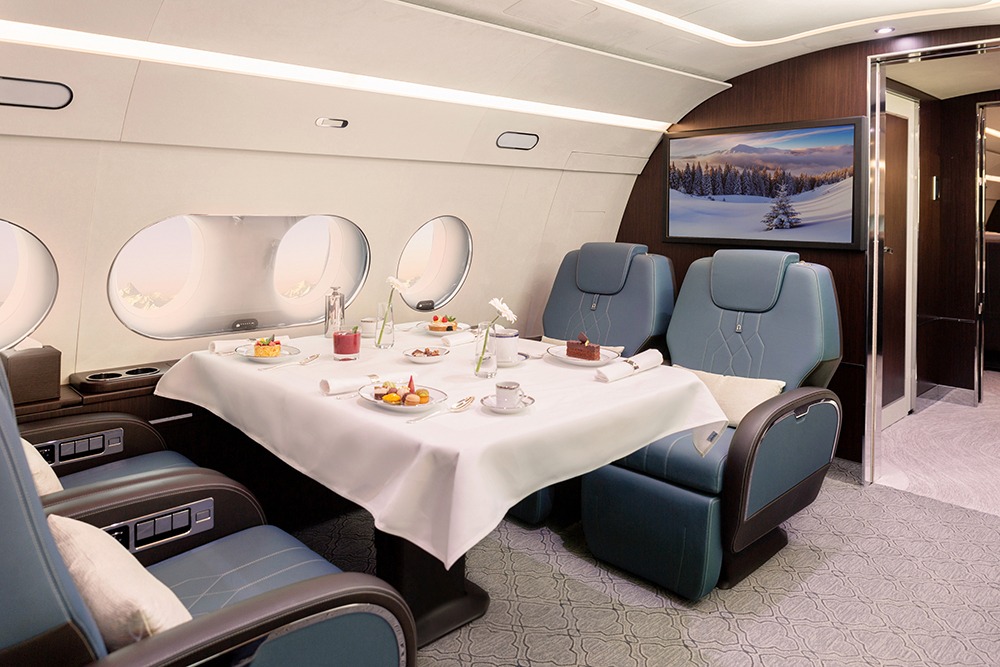
The next chapter
Comlux is a company that is not set with a veteran team focused on doing things the same way. The management team is, on average, 40 years old with a 15-year experience in the industry working to enhance the company’s products and processes using the latest technologies.
With the rapid growth and influx of projects, Comlux Completion has aggressively worked to train internally and promote from within. «Our internal Management Development program takes on 10-12 people per year and exposes them to all of our different sites and businesses. Not only does this enhance their future opportunities, but it also helps maintain the drive that is required to push Comlux forward,» concludes the spokesperson. The Head of Engineering, Head of Program Management, and Chief Operating Officer took their first jobs in aviation at Comlux Completion and have grown through the many opportunities the company provides.
Adam White, CEO Comlux Completion confirms: «I always say we want to hire people who want careers, not jobs. I am honored to lead a company that takes this mantra to heart and is small enough and diversified enough to offer it.»